Workshop on the Challenges to widespread adoption of 3D printing for manufacturing of high integrity, functional metal parts
Wednesday, 10th July 2019, AUT, City Campus,
The purpose of the workshop was to provide an update on the current status of Metal Additive Manufacturing (MAM), with particular emphasis on improving quality, process repeatability, specifications and applicable standards.
We will discuss what work needs to be done in NZ to accelerate the uptake of MAM by NZ manufacturers, thereby reducing future vulnerabilities to competitive and proprietary MAM operations. The benefits of MAM for producing, for example, parts of almost unlimited shape complexity are well known. The technology is often associated with the so-called fourth industrial revolution (Industry 4.0) and threatens to disrupt many traditional engineering design and manufacturing conventions. Indeed, commercial MAM operations and applications have increased significantly in recent years.
MAM processes are, however, highly challenging. In particular, parts of acceptable mechanical integrity and reliability can be highly dependent on a large number of machine, powder and design parameters, the independencies of which are not always well understood. This has been a major factor inhibiting the widespread adoption of MAM, with successful applications largely being developed via empirical methods, often in the absence of a full understanding of underlying metallurgical and scientific basis.
The workshop started with introductory comments by Patrick Conor, the chair of SMNZI, who outlined the need for appropriate characterisation of the properties of MAM products to ensure they are fit for purpose. The workshop then included three technical presentations by:
Dr Ben Withy from New Zealand’s Defence Technology Agency (DTA): Dr Withy is a research engineer in the fields of mechanical and materials engineering. Ben’s talk covered the role that NZDF sees for additive manufacturing in the next five years and the current obstacles to broader integration into the defence logistics capability. The talk touched on the policy and training requirements of NZDF, the challenges of integrating new manufacturing process into existing procurement systems and the technical and qualification challenges that are limiting the use of additive manufacturing from the obvious areas of support to legacy platforms and allowing “just in time” manufacture of spares.
Professor Judy Schneider from the Mechanical and Aerospace Engineering Department at the University of Alabama. Professor Schneider has led a large research group in MAM for the last several years and is also a Fellow of ASM International. Her presentation was titled ‘Achieving quality control of metal additive manufactured parts through improved understanding of the underlying microstructure’. The presentation summarized efforts to optimize post processes based on initial feedstock and build microstructures. She showed how this approach can form the basis for standardization specifications. In studies on Inconel alloys the effect of minor elements has been shown to strongly affect the microstructural development during post processing heat treatments, often containing non-equilibrium phases that are difficult to identify.
Mr Peter Sefont, Production Manager at Zenith Technica, a company that is actively engaged in pushing the boundaries of metal 3D Printing using Electron Beam Melting (EBM) technology. His presentation showed that the technology needs the intervention of qualified staff and requires a full qualification process in order to guarantee repeatable results. His presentation focused on the journey to reach certification, qualification and production with the EBM technology.
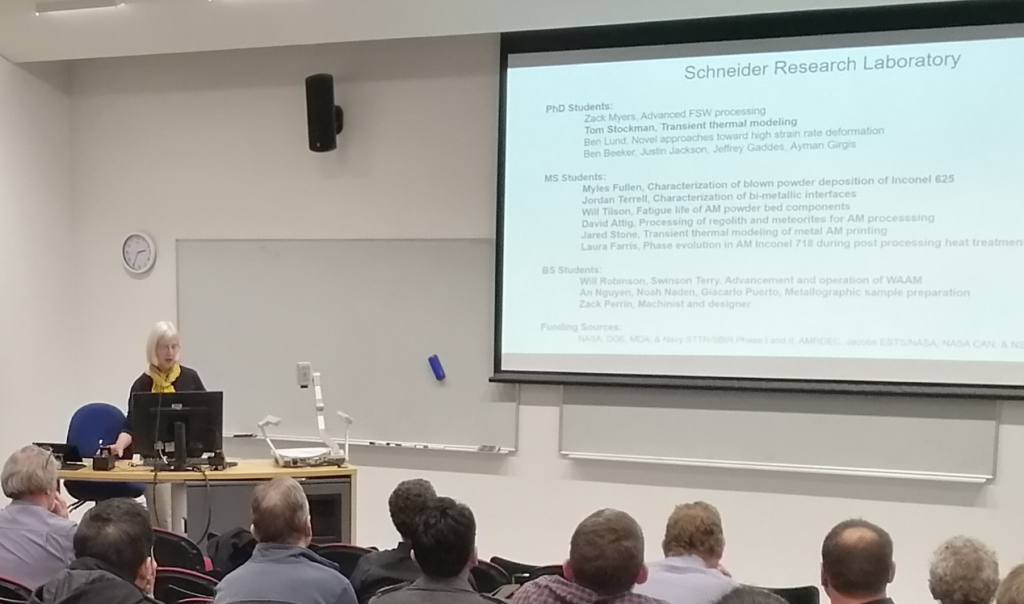